The source matters for the climate – new milestone for PET bottles: Yellow Bag share increased to 75 percent
Does the Yellow Bag matter for the climate? How does this formula work? With its cleverly crafted collection of plastic packaging via the dual system, Germany developed one of the best ideas for the circular economy. This collection system is the perfect source for creating new packaging through resource-conserving mechanical recycling. When 10 old plastic bottles land in the recycling system, 10 new bottles emerge. That is true recycling in the interests of a climate-friendly circular economy. When more plastic is kept in a closed loop, less new plastic has to be produced in climate-damaging ways. In addition, less plastic waste is generated.
Werner & Mertz and its cooperation partner ALPLA in the Recyclate Initiative have again scored a success for the genuine circular economy. For its proven Frosch PET bottles of 100 percent recycled plastic, the Mainz-based cleaning products manufacturer has increased the share of rPET from the Yellow Bag to 75 percent.
“The pioneering Werner & Mertz advances the technological exploitation of material from the Yellow Bag for high-quality packaging. More than four million PET bottles with the increased share of 75 percent Yellow Bag material have been placed in the market. We prove once again the feasibility of our approach in which we put used plastic from post-consumer waste collections through high-quality mechanical reprocessing, re-use it and thus keep it in a closed loop,” said Alexander Schau, packaging expert at Werner & Mertz. The remaining 25 percent of the material, which also is mechanically recycled, comes from European deposit bottle collection (Bottle to Bottle).
Technological progress and extensive knowledge make innovation possible
Thanks to the familiar high quality and unaltered look of the bottle, consumers do not see a difference. The step up to 75 percent was made possible by a state-of-the-art sorting facility and knowledge acquired from continuous monitoring of the delivered PET bales in the recycling plant.
ALPLArecycling was able to increase sorting efficiency with ultra modern software and computer technology which allow more precise sorting at higher speed. “Plastic is valuable material that should get the best possible re-use in a closed loop. We manage to do that only by continuously developing our recycling processes and investing in the latest sorting technology. Our many years of cooperating with Werner & Mertz on increasing the proportion of recycled material from the Yellow Bag is a great example of joint implementation of progressive recycling projects,” said Dietmar Marin, Managing Director Recycling Division at ALPLA.
Packaging experts from Werner & Mertz examine the bales of used plastic delivered to the recycling plant. At regular intervals on site, they analyze the materials and their quality in PET bales awaiting recycling. Knowledge of this particular waste stream goes into process development.
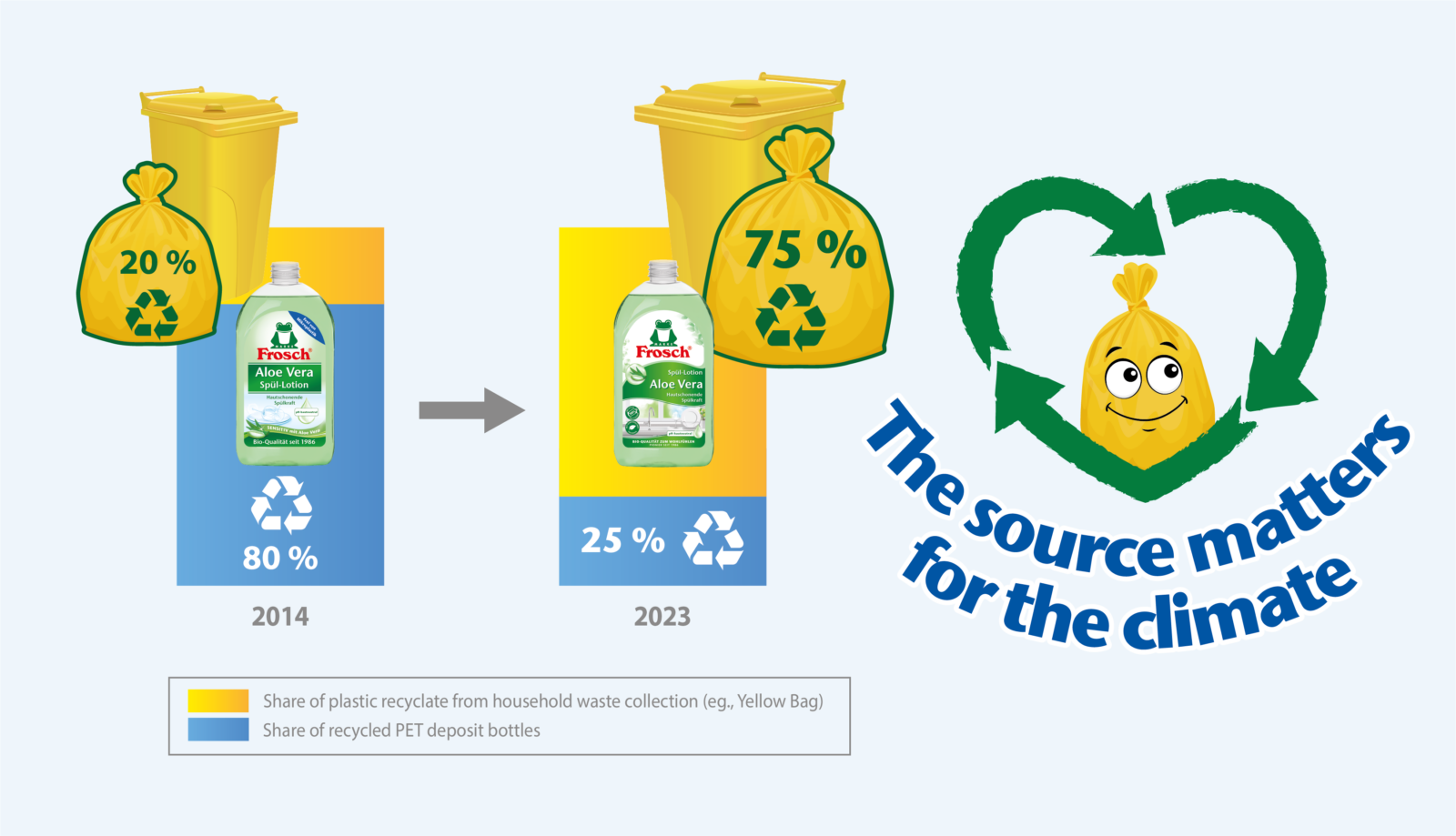
Successful cooperation
With yet another increase in the share from household waste collections, Werner & Mertz and ALPLA continue the success story of their cooperation. The Recyclate Initiative was launched back in 2012 by Werner & Mertz, together with ALPLA and other cooperation partners from the entire value chain. Committed to using Post-Consumer Recyclate (PCR), the Initiative partners say that used plastic (Post-Consumer Recyclate or PCR) from household waste collections should be utilized as input material, reprocessed after use, re-used as recycled and recyclable material, and thereby kept in a closed loop. In 2014 the initiative succeeded in producing PET bottles for the well-known Frosch brand from 100 percent PCR, 20 percent of which came from the Yellow Bag. In February 2021 the next increase to 50 percent followed and in 2023 the share reached 75 percent.
The source matters for the climate
Where the plastic packaging comes from is vitally important
+ Mechanical Recycling
As proven in practice millions of times, used plastic from the Yellow Bag can be sorted by type and recycled cleanly in a high-quality upcycling process. Given its low melting point, plastic is well-suited for use again and again. Mechanical recycling of plastic is the most direct and energy-efficient form of the circular economy in our industry.
– New Plastic
In a study conducted by ETH Zürich1 in 2022, analysts concluded: “twice as much fossil carbon is combusted as fuel for plastics production than contained as feedstock in plastics.”
The alarming results are particularly noteworthy because research to date has concentrated on the environmental pollution that occurs with the disposal of plastic. Those damages alone are enormous. The incineration of plastic packaging, the primary means of disposal in Germany and other European countries, generates on average three grams of CO2 for every gram of plastic. Moreover, burning the plastic is a tremendous waste of a valuable raw material.
The fact that the manufacture of new plastic generates even more greenhouse gas emissions than incineration means the carbon footprint of virgin plastic is much worse than previously assumed. The major factor for the enormous amounts of energy used in production, according to researchers, is the continuously increasing use of coal-generated electricity. That applies primarily for the booming plastic economy in emerging markets in China, India and Indonesia, where the required energy for new plastic comes mainly from climate-damaging coal-powered plants. Many EU countries and Western industrialized countries, the study reports, have outsourced energy-intense manufacturing of plastic to those countries.
– Pyrolysis
In pyrolysis, the used plastic is decomposed into its petrochemical components at temperatures up to 1,500 degrees Celsius so that it can be processed into plastic again with help from new oil.
The many variations of pyrolysis—also known as “chemcycling” or “chemical recycling”—have one thing in common. They require a lot of energy, for example, to obtain plastic from pyrolysis oil. A study by a major environmental organization² documents the poor track record of this process. To convert one metric ton of used plastic into plastic, pyrolysis needs one metric ton of fossil fuel as an additional energy supplier. Independent experts therefore see pyrolysis not as a variety of recycling, but rather as a variant of incinceration.
This source does not protect the climate. Every gram of incinerated plastic generates about three grams of CO2. On top of that, a large quantity of material is lost to pyrolysis. In most cases, the small amount of pyrolysis oil obtained can be processed further only after additional, time-consuming chemical cleaning.