The Source Matters for the Climate!
We use material from the Yellow Bag in our packaging and thereby contribute greatly to climate protection.
Does the Yellow Bag matter for the climate? How does this formula work? With its cleverly crafted collection of plastic packaging via the dual system, Germany developed one of the best ideas for the circular economy.
This collection system is the perfect source for creating new packaging through resource-conserving mechanical recycling. When 10 old plastic bottles land in the recycling system, 10 new bottles emerge. That is true recycling in the interests of a climate-friendly circular economy. When more plastic is kept in a closed loop, less new plastic has to be produced in climate-damaging ways. In addition, less plastic waste is generated. The Yellow Bag material collection is finally what consumers have long awaited, that is, the starting point of a truly closed loop.
Mechanical Recycling 👍
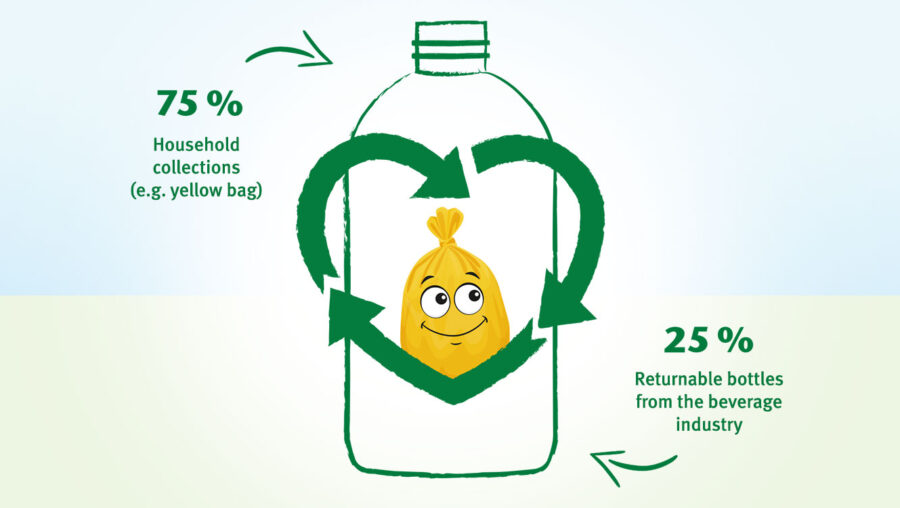
Through mechanical recycling of plastic packaging and the use of Yellow Bag material, we have been setting new standards for years. As early as 2014, the PET bottles for Frosch products were made completely of recycled material. At first 20 percent came from the Yellow Bag and the remaining 80 percent from European deposit bottle collections (Bottle to Bottle). In 2021 Werner & Mertz in cooperation with ALPLA raised the recycled plastic portion from the Yellow Bag to 50 percent. In 2023 the next milestone was reached with an increase to 75 percent—a new record in international comparison.
As proven in practice millions of times, used plastic from the Yellow Bag can be sorted by type and recycled cleanly in a high-quality upcycling process. Given its low melting point, plastic is well-suited for use again and again. Mechanical recycling of plastic is the most direct and energy-efficient form of the circular economy in our industry.
New Plastic ⛔
In a study conducted by ETH Zürich in 2022, analysts came to the alarming conclusion: “twice as much fossil carbon is combusted as fuel for plastics production than contained as feedstock in plastics.”
The results are particularly noteworthy because research to date has concentrated on the environmental pollution that occurs with the disposal of plastic. Those damages alone are enormous. The incineration of plastic packaging, the primary means of disposal in Germany and other European countries, generates on average three grams of CO2 for every gram of plastic. Moreover, burning the plastic is a tremendous waste of a valuable raw material.
The fact that the manufacture of new plastic generates even more greenhouse gas emissions than incineration means the carbon footprint of virgin plastic is much worse than previously assumed. The major factor for the enormous amounts of energy used in production, according to researchers, is the continuously increasing use of coal-generated electricity. That applies primarily for the booming plastic economy in emerging markets in China, India and Indonesia, where the required energy for new plastic comes mainly from climate-damaging coal-powered plants. Many EU countries and Western industrialized countries, the study reports, have outsourced energy-intense manufacturing of plastic to those countries.
Pyrolysis ⛔
In pyrolysis, the used plastic is decomposed into its petrochemical components at temperatures up to 1,500 degrees Celsius so that it can be processed into plastic again with help from new oil.
The many variations of pyrolysis—also known as “chemcycling” or “chemical recycling”—have one thing in common. They require a lot of energy, for example, to obtain plastic from pyrolysis oil. A study by a major environmental organization² documents the poor track record of this process. To convert one metric ton of used plastic into plastic, pyrolysis needs one metric ton of fossil fuel as an additional energy supplier. Independent experts therefore see pyrolysis not as a variety of recycling, but rather as a variant of incinceration.
This source does not protect the climate. Every gram of incinerated plastic generates about three grams of CO2. On top of that, a large quantity of material is lost to pyrolysis. In most cases, the small amount of pyrolysis oil obtained can be processed further only after additional, time-consuming chemical cleaning.